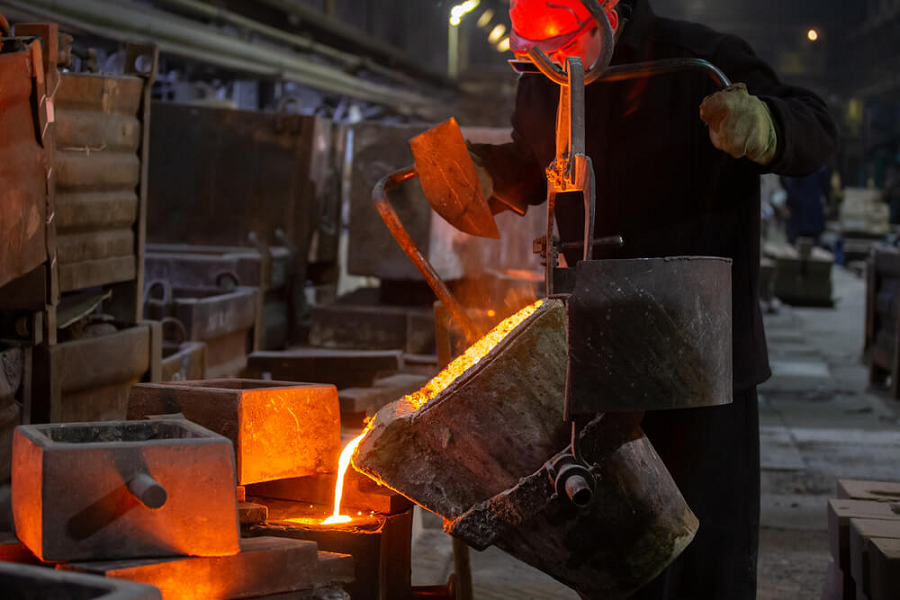
Metal casting is a versatile and indispensable technique that allows artisans and manufacturers alike to create customized metal objects with precision and uniqueness. This process enables the production of everything from intricate sculptures to functional mechanical components. In this article, we will explore the art and science of metal casting, shedding light on its various applications, materials involved, and the steps required to produce a successful cast.
The Essence of Metal Casting
Metal casting, at its core, is the process of pouring molten metal into a mold to create a specific shape as the metal cools and solidifies. This technique allows for the production of complex and customized designs that may be challenging or impossible to achieve through other methods. The key elements of metal casting include the choice of metal, the creation of a mold, and the casting process itself.
Choice of Metal
One of the fundamental decisions in metal casting is selecting the appropriate metal alloy for the desired application. Different metals have distinct properties, such as strength, ductility, and corrosion resistance. Common metals used in casting include aluminum, bronze, brass, iron, and steel. Each metal has unique characteristics that make it suitable for specific applications.
Creating the Mold
The mold is a crucial element in metal casting, as it defines the final shape of the cast object. There are several methods for creating molds, including sand casting, investment casting, and die casting. The choice of molding method depends on factors such as the complexity of the design, the quantity of parts needed, and the desired level of detail:
Sand Casting
Sand casting is a versatile and cost-effective method suitable for producing large and small objects. It involves creating a mold cavity in specially prepared casting sand, often using a pattern or core. After the metal is poured into the mold and cools, the sand mold is removed, revealing the cast object.
Investment Casting
Investment casting, also known as lost-wax casting, is ideal for intricate and highly detailed designs. It begins with the creation of a wax or plastic pattern, which is coated in a ceramic shell. The wax is then melted away, leaving a cavity in the ceramic shell. Molten metal is poured into this cavity, resulting in a precise cast object.
Die Casting
Die casting is a high-pressure method used for producing large quantities of small to medium-sized parts with consistent quality. In this process, molten metal is forced into a metal mold under pressure. Die casting is commonly used in the automotive, electronics, and consumer goods industries.
The Casting Process
The actual casting process involves melting the chosen metal and pouring it into the prepared mold. It is essential to ensure that the metal flows evenly and fills the mold completely to avoid defects. Temperature control, gating systems, and venting are critical aspects of achieving a successful cast. Once the metal solidifies, the mold is removed, and the casting is finished and often undergoes post-processing, such as machining or surface treatments.
Applications of Metal Casting
The applications of metal casting are vast and varied, spanning multiple industries:
Industrial Machinery
Metal casting is instrumental in producing components for industrial machinery, including gears, housings, and valve bodies.
Art and Sculpture
Many artists use metal casting to create sculptures and artworks of all sizes and complexities.
Jewelry and Ornaments
The jewelry industry relies on casting to produce intricate pieces, from rings and pendants to decorative ornaments.
Automotive and Aerospace
Critical components for vehicles, aircraft, and spacecraft, such as engine parts and structural elements, are often created through metal casting.
Metal casting is a dynamic and versatile technique that bridges the worlds of art and industry. It offers a pathway to turn creative visions into reality while also serving as a cornerstone of modern manufacturing. Understanding the nuances of metal casting, from selecting the right metal to mastering the casting process, empowers artisans and engineers alike to bring their unique designs and ideas to life. Whether for artistic expression or industrial innovation, metal casting remains a key to unlocking endless possibilities in the world of metalworking.